Introduction of Kyoyuzen Dyeing Techniques
Four Kyoyuzen dyeing techniques to be handed down to future generations.
Kyoyuzen dyeing vibrantly colors the aesthetics that form the basis of nature throughout the four seasons, and the spirits in Japan. There are four main styles that make up its breakthrough techniques, and various yuzen-dyed products have been produced through development resulting from the competition of each technique. These four techniques are very important assets that we must hand down to future generations for Kyoyuzen dyeing. They are assets in Japan, and eventually those of the world.
1. Freehand Dyeing
"Freehand Dyeing" has a history of more than 300 years to today. As many as approximately 20 processes are required until the completion of one kimono. If applying a tie-dyeing process, as many as one year may be needed until completion.
Careful hand work, such as design, preliminary sketches, and pattern coloring (sashi yuzen), are performed under the full specialization system, where specialized vendors and craftspeople are assigned to each field. A high degree of skill is required for every craftsman.
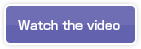
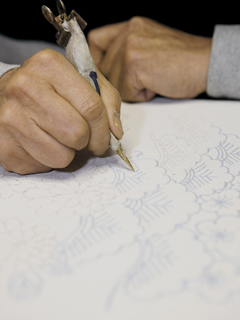
Extracting glue and drawing the design based precisely on the preliminary sketch is called "Itome", which helps prevent dye from seeping out into other portions when coloring the pattern.
Draw the preliminary sketch directly on temporarily tailored fabric using the blue juice of Asiatic dayflower.
In the pattern coloring process, dozens of dye types are used, and the pattern is colored using writing and painting brushes.
Gold processing includes several techniques, such as gold tying (see the photo), impressed gold foil, stamping foil, and gold dust.
2. Stencil Dyeing
As named, "Stencil Dyeing" introduces stencils for dyeing. Just as many stencils as the number of colors are necessary, and dozens to hundreds of stencils are used for one kimono as gradation is also applied in some cases. Various techniques, such as impressing, and spray dyeing, are used on a dyeing board, and excellent skill is employed during all of these processes.
This is the work that cannot be completed without professional skill, where, for example, one craftsman is responsible for dozens of stencils, and a skill to dye in the same color density is also required.
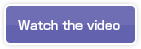
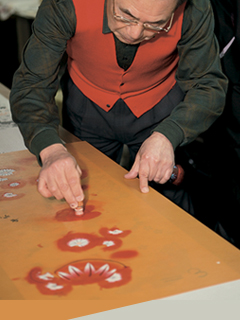
There are various techniques, such as impressing, and piece (spray) dyeing on a dyeing board. The photo shows when gradation is being applied. Use different types of dedicated gradation brushes (round brushes) skillfully for each purpose, and generate contrasting densities.
The stencil dyeing is also called "Itaba (Board) Yuzen", as it is performed by pasting fabric on a long single board. The length of a board is approximately 6 meters, and two sides of the board are used for one kimono.
Pull-brush dyeing is performed by pulling both ends of fabric using a wooden panel, and applying thin sticks at even intervals to stretch the fabric tightly.
Quickly dye fabric using brushes to achieve uniform dyeing. Extreme care is taken with regards to differences in temperature and humidity according to the season.
3. Textile Printing Dyeing
"Textile Printing Dyeing" can be used to dye patterns uniformly without joints by using a machine instead of manual processing.
Prepare as many printing rolls with patterns engraved on their surfaces as the number of colors. Align the rolls so that fabric is dyed based precisely on the design, and set up. This alignment is harder as the number of colors increases, and requires highly skilled technique. Even though the machine is used for dyeing, people still pay extreme care in the process, and craftsmen always give careful attention to every step.
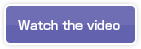
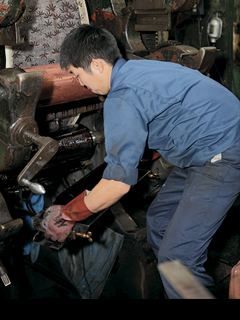
Set rolls properly so that fabric is to be dyed according to the color combination finely specified for each portion. Perform test printing numerous times to check that there is no mistake in color.
Rolls are made of copper, and the weight of a roll is 10 to 15 kg. One roll is required for per color. Ask specialized vendors to apply engraving based on the design.
While correcting expansion and contraction of fabric entering the machine, always check the pattern match.
Fabric is going to be dyed in the same manner of rotary press. For Komon dyeing, the same pattern appears sequentially each time the roll rotates one revolution.
4. Digital Printing
"Digital Printing" can be used for dyeing using a large printer. Digital graphic pens instead of writing brushes are used to color the pattern. For flowers, each flower petal is carefully drawn by hand, and various settings needed for printing are conducted on digital graphics. Gold processing after encouraging the color effect through steaming and washing, is the big moment for craftsmen involving in Itaba (board) yuzen dyeing. Work that can be done only by experienced craftsmen has been impressively blended with computer technology.
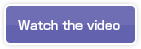
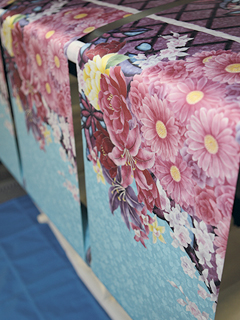
Dyeing is performed using a printer. It is generally called ink jet, but dyes are used instead of ink.
Load the design on digital graphics, and extract the lines of the design to start coloring. Enter the color sample number to paint colors.
Color samples
Gold processing is applied on a dyeing board. Matching the pattern after steaming and washing processes is very difficult, and is a challenging stage for craftsmen.
The secondary use of information and images provided by our website without our permission,
including duplication and/or diversion, is strictly prohibited.